KRR045DPC19NNNNN3C2NGA6NKNBNNNNNN sauer danfoss pump
KRR045DPC19NNNNN3C2NGA6NKNBNNNNNN sauer danfoss pump

- Product Details
- Applicable Scene
The rapidly evolving field of industrial automation is transforming the way machinery, such as hydraulic oil pumps, operates and is maintained. By integrating the Internet of Things (IoT) with predictive maintenance systems, manufacturers can not only enhance the efficiency of hydraulic oil pumps but also extend their lifespan, reduce downtime, and lower costs associated with unplanned maintenance. This article discusses the design considerations for hydraulic oil pumps that are compatible with IoT-enabled predictive maintenance systems.
KR-R-045D-PC-19-NN-NN-N-3-C2NG-A6N-KNB-NNN-NNN
KRR045DPC19NNNNN3C2NGA6NKNBNNNNNN
One of the fundamental elements of designing hydraulic oil pumps for IoT integration is the selection of suitable sensors. These sensors play a critical role in monitoring various operational parameters such as pressure, temperature, vibration, and fluid levels. By installing advanced sensors, engineers can gather real-time data on the pump’s performance, which can be used to identify potential issues before they escalate into major failures.
83030468
Data analytics is another crucial aspect of enabling predictive maintenance systems. The real-time data collected from the sensors can be transmitted to a cloud platform for analysis. Here, powerful algorithms can process the data to identify patterns and trends, offering insights into the pump’s operational health. For instance, an increase in vibration levels may indicate wear and tear on internal components, prompting proactive maintenance actions. This predictive capability helps manufacturers shift from a reactionary maintenance approach to a more efficient predictive maintenance regime.
Moreover, the design of hydraulic oil pumps must consider connectivity features. Incorporating communication protocols such as MQTT or HTTP allows pumps to connect seamlessly with IoT platforms. This connectivity not only facilitates data transfer but also enables remote monitoring and management of the pumps from any location. Operators can receive alerts and notifications regarding the pump’s status, further enhancing their ability to intervene before minor issues develop into costly repairs.
The design phase should also emphasize energy efficiency. Hydraulic oil pumps that consume less energy contribute to lower operational costs and a reduced carbon footprint. Integrating IoT technology can help achieve this by optimizing the pump’s operation based on real-time data analytics. For example, the system can automatically adjust the pump’s flow rate based on the demand, thus conserving energy without compromising performance.
Another aspect to consider in the design process is the user interface. Providing operators with an intuitive dashboard that visualizes the data collected from the hydraulic pumps is essential. A well-designed interface can help users quickly interpret the performance metrics and make informed decisions regarding maintenance schedules and operational adjustments.
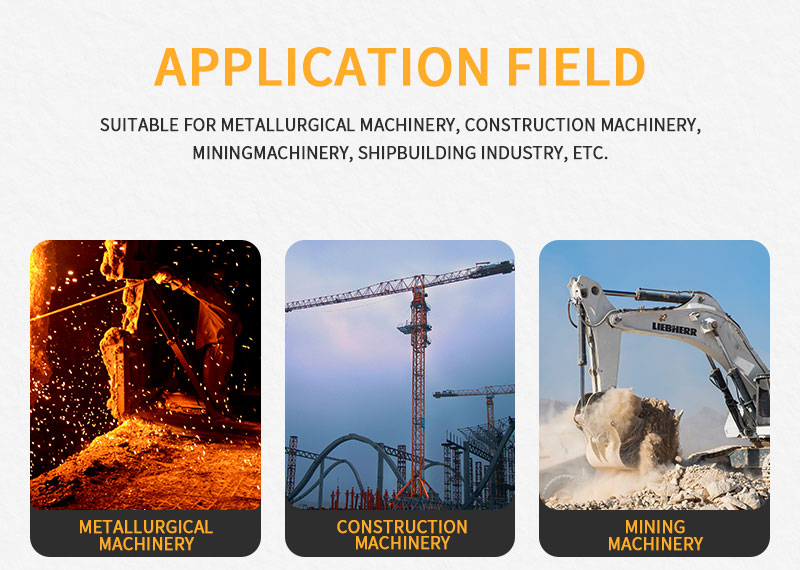
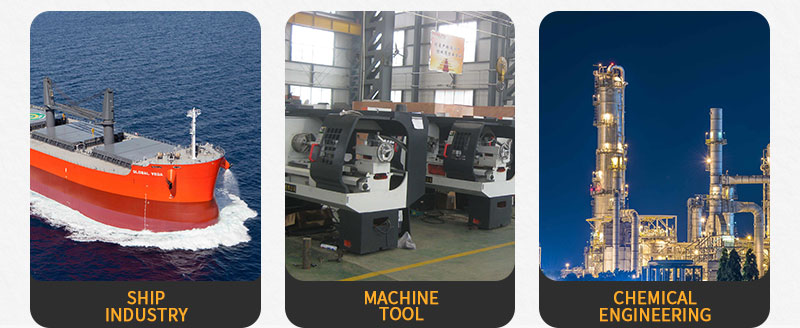