KRR038CLS2420NNN3C3AGA6NAAANNNNNN danfoss pump
KRR038CLS2420NNN3C3AGA6NAAANNNNNN danfoss pump

- Product Details
- Applicable Scene
In recent years, the industrial sector has witnessed a significant transformation with the advent of digital technologies, and one of the most promising innovations is the concept of digital twins. A digital twin is a virtual representation of a physical asset, system, or process that enables real-time monitoring, analysis, and optimization. For companies like Sauer Danfoss, known for their high-performance pumps and hydraulic solutions, leveraging digital twins can lead to enhanced performance, reduced downtime, and improved operational efficiency.
KR-R-038C-LS-24-20-NN-N-3-C3AG-A6N-AAA-NNN-NNN
KRR038CLS2420NNN3C3AGA6NAAANNNNNN
Digital twins can be particularly beneficial in optimizing the performance of Sauer Danfoss pumps in several ways. First, they enable companies to continuously monitor the operational parameters of pumps. This involves the collection of data from various sensors installed in the pumps, such as pressure, flow rate, temperature, and vibration. By analyzing this data, a digital twin creates a comprehensive model that reflects the current state of the physical pump, allowing for insights into performance trends and potential issues.
80002375
One of the primary advantages of using digital twins is predictive maintenance. Traditional maintenance practices often rely on fixed schedules or responding to failures after they occur, which can lead to unnecessary downtime and operational costs. With a digital twin, Sauer Danfoss can employ predictive analytics to forecast potential failures before they happen. By analyzing historical data and current performance metrics, the digital twin can indicate when a component is likely to fail, allowing operators to conduct maintenance proactively and minimize unexpected interruptions in service.
Moreover, digital twins facilitate real-time simulation and scenario analysis. Engineers and operators can experiment with different operational conditions within the digital environment without affecting the actual pump. For instance, modifications such as adjusting flow rates or operating pressures can be tested virtually to determine their impact on efficiency and performance. This not only enhances the design phase of new pump systems but also assists in optimizing existing setups for better energy efficiency and operational effectiveness.
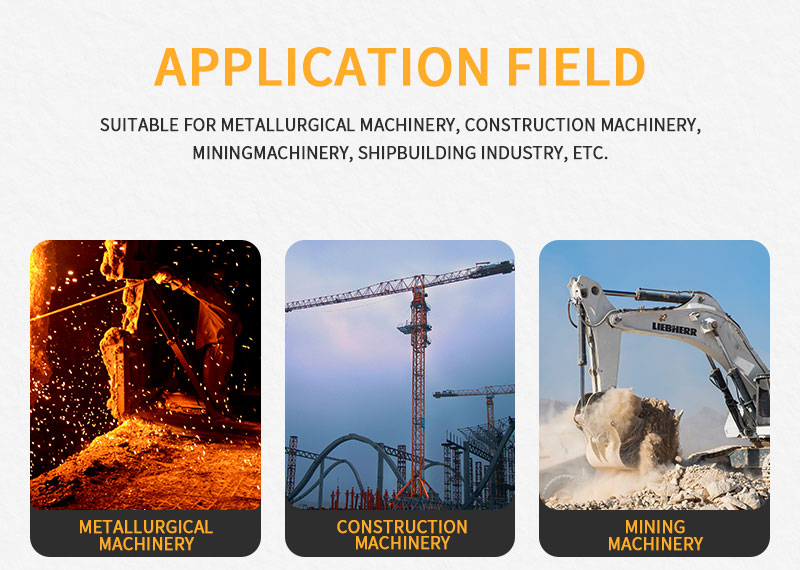
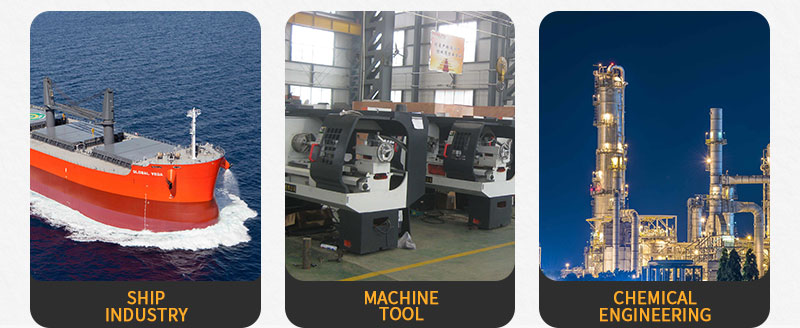