LRR030DEG2120NNK3K2BGA6NPLBNNNNNN axial piston pump
LRR030DEG2120NNK3K2BGA6NPLBNNNNNN axial piston pump

- Product Details
- Applicable Scene
In the world of manufacturing, injection molding stands as a cornerstone technology for producing high-quality plastic parts. The process requires consistent and precise control over various parameters, such as pressure and flow rate. Among the various components that enhance the performance of injection molding machines, piston pumps play a significant role in ensuring high precision and efficiency. This article explores how piston pumps contribute to high-precision injection molding and why they are preferred in many applications.
LR-R-030D-EG-21-20-NN-K-3-K2BG-A6N-PLB-NNN-NNN
LRR030DEG2120NNK3K2BGA6NPLBNNNNNN
Piston pumps are known for their ability to generate high pressures and maintain a steady flow rate. Unlike gear or diaphragm pumps, which may exhibit fluctuations in performance, piston pumps provide a constant discharge pressure that is crucial for the injection process. This steady pressure is particularly important when molding intricate components, where any inconsistency in material flow can lead to defects such as surface imperfections, incomplete fillings, or misalignment.
83067192
One of the key advantages of piston pumps is their ability to handle various types of materials, including those with high viscosities. In injection molding, the choice of thermoplastic or thermosetting materials can significantly influence the quality of the finished product. Piston pumps can effectively manage these materials by delivering a precise volume of resin or other substances into the mold cavity, ensuring that every cycle is uniform. This capability not only enhances product quality but also reduces waste, making the process more sustainable and cost-effective.
Another factor contributing to the precision of piston pumps in injection molding is their design. Piston pumps typically feature a robust construction that minimizes wear and tear, thereby maximizing their lifespan and reducing maintenance costs. Furthermore, they can be equipped with advanced control systems that monitor and adjust operational parameters in real-time. This integration allows manufacturers to fine-tune the injection molding process for different materials and part designs, thereby achieving unprecedented levels of accuracy and repeatability.
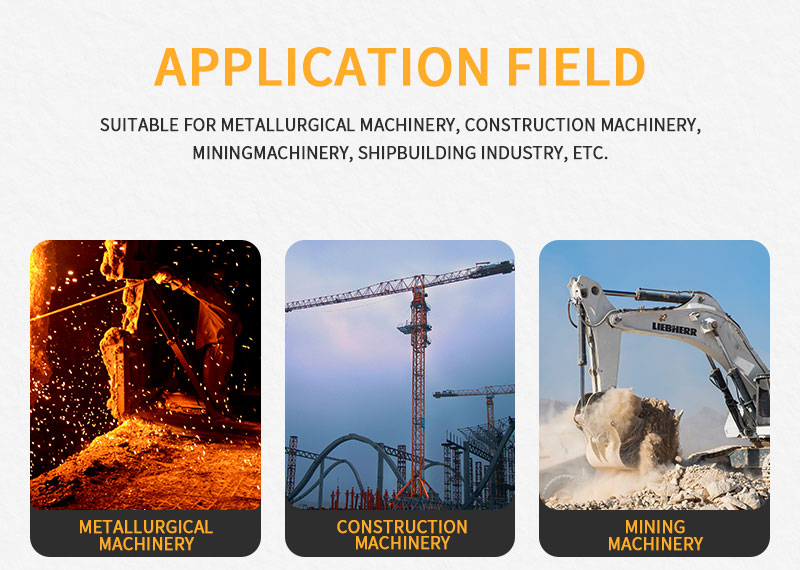
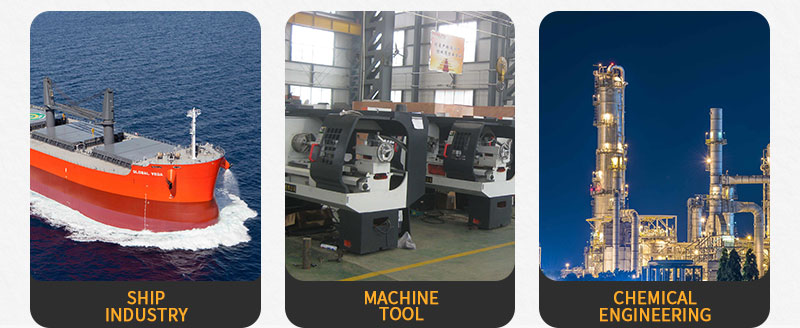