90R250KA5AB80T3C8K03NNN424224 hydraulic pump
90R250KA5AB80T3C8K03NNN424224 hydraulic pump

- Product Details
- Applicable Scene
Piston pumps are widely used in various industrial applications due to their efficiency and reliability. However, like any mechanical device, they are prone to failure if not properly maintained or operated. Understanding the common causes of piston pump failure and implementing preventive measures can significantly extend their lifespan and ensure optimal performance.
90R250-KA-5-AB-80-T-3-C8-K-03-NNN-42-42-24
90R250KA5AB80T3C8K03NNN424224
One of the primary causes of piston pump failure is wear and tear of the internal components. Piston pumps consist of various moving parts that are subject to friction and stress during operation. Over time, this wear can lead to decreased performance and eventual failure. To prevent this, regular inspections and maintenance are essential. Lubricating the moving parts and replacing worn components can help mitigate this issue.
83018376
Another common cause of failure is contamination of the hydraulic fluid. Dirt, debris, and other contaminants can enter the pump, causing damage to the internal parts and leading to a breakdown. To minimize this risk, it is crucial to maintain a clean operating environment and implement effective filtration systems. Regularly checking fluid quality and replacing it as needed can also help prevent contamination-related failures.
Overheating is another significant factor that can lead to piston pump failure. If the pump operates at temperatures beyond its design limits, it can cause seals to degrade, fluids to break down, and components to warp. Ensuring that the pump is adequately cooled and not overloaded can help reduce the risk of overheating. Monitoring temperature levels and implementing cooling systems when necessary can be effective preventive measures.
Incorrect installation and alignment can also contribute to piston pump failure. If the pump is not installed correctly, it can cause excessive stress on components and lead to early wear. Proper alignment and installation according to the manufacturer’s guidelines are critical. Regular audits and configuration checks can help ensure that the setup is optimal.
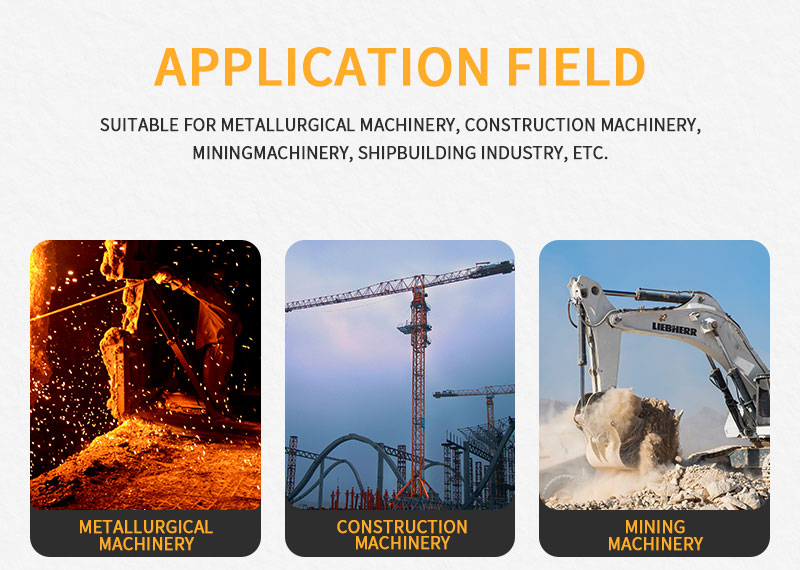
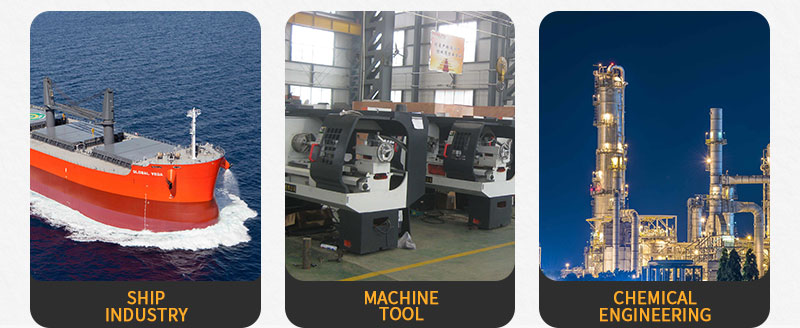