KRR045DLS2020NNN3K2NFA6NPLBNNNNNN high pressure pump
KRR045DLS2020NNN3K2NFA6NPLBNNNNNN high pressure pump

- Product Details
- Applicable Scene
In the evolving field of aerospace technology, the quest for more efficient propulsion systems has driven significant research and development. As experimental aerospace technologies continue to advance, one of the critical components that require meticulous design and optimization is the hydraulic oil pump. This article explores the importance of hydraulic oil pumps in aerospace propulsion systems, the design considerations involved, and their impact on efficiency and performance.
KR-R-045D-LS-20-20-NN-N-3-K2NF-A6N-PLB-NNN-NNN
KRR045DLS2020NNN3K2NFA6NPLBNNNNNN
Hydraulic systems are pivotal in aerospace applications, providing the necessary force to operate various components such as flight controls, landing gear, and propulsion systems. In experimental propulsion technologies, efficient and reliable hydraulic oil pumps play a crucial role in ensuring that these systems operate smoothly under diverse environmental conditions and operational challenges.
7004168S
One of the primary considerations in designing hydraulic oil pumps for aerospace applications is the specific requirements of the propulsion system. These requirements often entail high pressures, variable flow rates, and the ability to operate reliably in extreme temperatures and altitudes. To meet these demands, engineers must choose appropriate materials that can withstand these conditions while minimizing weight to enhance overall vehicle performance.
Another key aspect of hydraulic oil pump design is the efficiency of the system. In propulsion technologies, minimizing energy loss is essential. The design must optimize the hydraulic circuit to reduce friction losses, thereby improving the overall efficiency of the pump. Advanced computational fluid dynamics (CFD) modeling tools can be employed to simulate fluid flow within the pump, allowing engineers to refine designs before physical prototypes are created.
Moreover, noise and vibration levels are critical in aerospace applications. The design of hydraulic oil pumps must consider acoustic properties and minimize vibrations that could lead to structural fatigue or affect onboard instrumentation. Utilizing noise-dampening materials and optimizing the geometry of the pump can contribute to a quieter system, which is particularly vital for manned spacecraft and aircraft.
As aerospace technologies move toward electrification and hybrid propulsion systems, the role of hydraulic oil pumps may evolve. It is essential for modern designs to anticipate future technological trends, such as the integration of electric actuators and smart control systems. Implementing digital sensors and controls in hydraulic pumps can lead to improved performance feedback and dynamic regulation, enhancing system responsiveness and reliability.
Testing and validation of hydraulic oil pumps under real operational conditions are necessary to ensure safety and reliability in aerospace applications. Rigorous testing protocols should be established, including simulating extreme conditions that components may encounter in flight. This testing phase is crucial to identify potential failure modes and refine design based on empirical data.
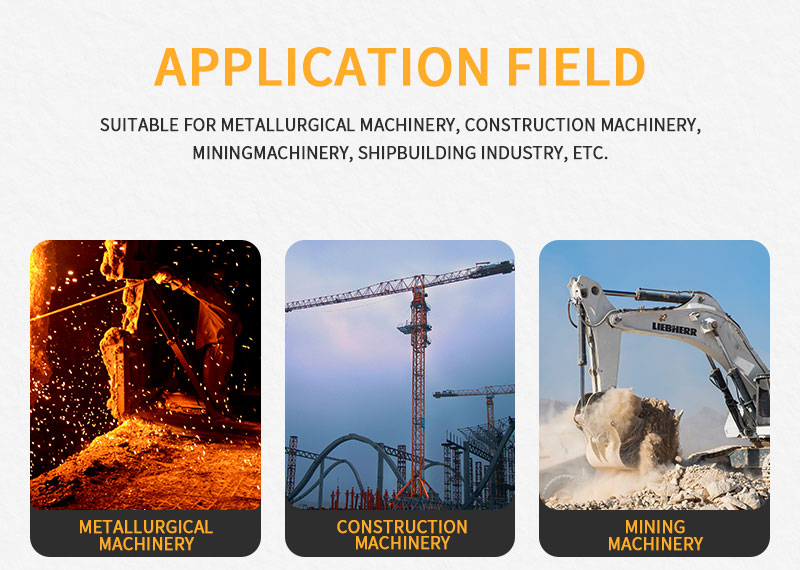
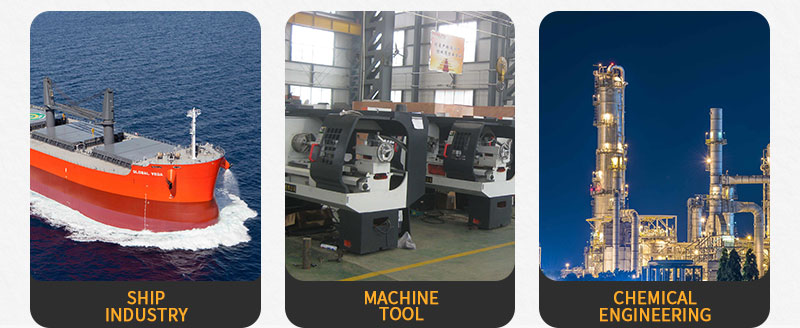