KRR045DLS2120NNN3K2NFA6NPLBNNNNNN piston pump
KRR045DLS2120NNN3K2NFA6NPLBNNNNNN piston pump

- Product Details
- Applicable Scene
In recent years, the integration of hydraulic systems in robotics has revolutionized the design and functionality of machines used in high-risk industrial environments and rescue operations. Among the critical components of these hydraulic systems, hydraulic oil pumps play an essential role in ensuring that machinery operates smoothly and efficiently. This article explores the design considerations for hydraulic oil pumps specifically tailored for high-risk industrial and rescue robotics, focusing on safety, reliability, efficiency, and adaptability.
KR-R-045D-LS-21-20-NN-N-3-K2NF-A6N-PLB-NNN-NNN
KRR045DLS2120NNN3K2NFA6NPLBNNNNNN
One of the primary challenges in designing hydraulic oil pumps for high-risk applications is the need for robustness. Industrial environments often present extreme conditions, such as temperature fluctuations, exposure to chemicals, and physical impacts from heavy machinery. Similarly, rescue robotics may operate in hazardous locations, such as disaster zones, where pumps must withstand dust, moisture, and potential debris. To address these conditions, engineers must select materials that not only provide strength and durability but also exhibit resistance to corrosion and wear.
7004119S
Safety is paramount when designing hydraulic systems for rescue and high-risk environments. A failure in the hydraulic system could lead to catastrophic consequences, putting both the robotic system and human operators at risk. Therefore, redundancy in design is critical. Incorporating features like dual pumps, backup power supplies, and fail-safe mechanisms can ensure continued operation even if one component fails. Additionally, implementing pressure relief valves and sensors to monitor oil levels and temperatures can prevent overheating and system overloads, enhancing overall safety.
Efficiency is another vital consideration. Hydraulic pumps should be designed to deliver optimal performance while consuming minimal energy. This requires a careful selection of pump types—gear, vane, or piston pumps—based on the specific needs of the robotic application. Engineers should conduct simulations and analyses to fine-tune the design for maximum flow rate and minimal energy loss, taking into account the varying loads and operational speeds encountered in dynamic environments.
Adaptability is crucial for hydraulic oil pumps used in rescue robotics. These systems often face unpredictable challenges, such as navigating through unstable terrains or lifting heavy debris. Designing pumps that can adjust their output pressure and flow based on real-time data allows robots to perform tasks more effectively. Incorporating smart technologies, such as IoT sensors and machine learning algorithms, enables hydraulic systems to optimize performance and respond to changing conditions without the need for manual intervention.
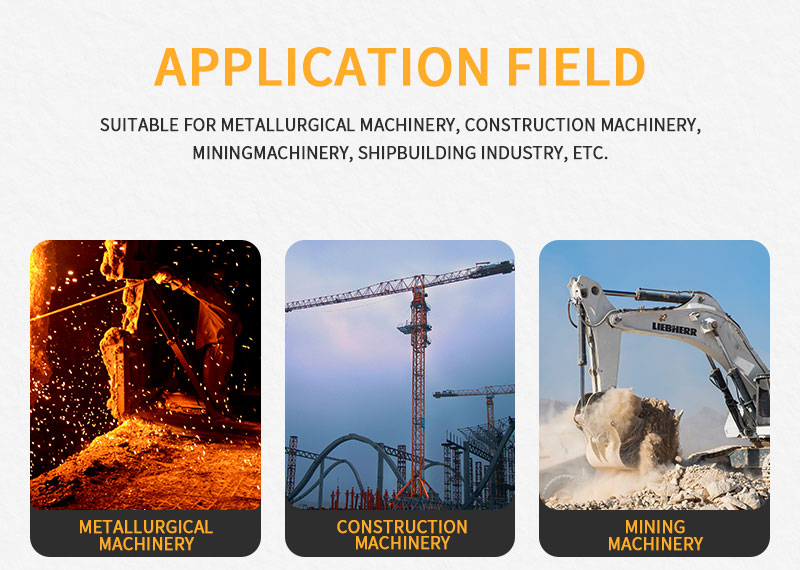
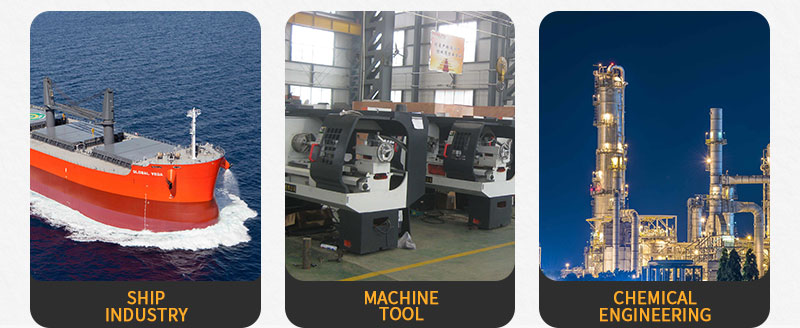